5
Теплообменная аппаратура
Теплообменные аппараты предназначены
для нагревания, охлаждения, испарения, конденсации технологических сред.
Большинство процессов химической технологии связано с необходимостью подвода или
отвода тепла, поэтому теплообменная аппаратура составляет 15-18% парка
оборудования предприятий химической промышленности.
Теплообменные аппараты
классифицируют по следующим признакам:
1.По конструкции теплообменной поверхности: изготовленные из труб
(кожухотрубчатые, "труба в трубе", оросительные, погружные
змеевиковые, воздушного охлаждения); изготовленные из листового материала
(пластинчатые, спиральные, сотовые); изготовленные из неметаллических
материалов (графита, пластмасс, стекла);
2.По назначению: подогреватели, холодильники, испарители,
конденсаторы;
3.По направлению движения теплоносителей: прямоточные, противоточные, перекрестного тока.
Общие рекомендации по
выбору конструкции теплообменника и схемы движения теплоносителей:
- при высоких давлениях
теплоносителей предпочтительнее кожухотрубчатые теплообменники, причем в
трубное пространство направляется теплоноситель с более высоким давлением;
- коррозионный теплоноситель в трубчатых
теплообменниках следует направлять по трубам, т.к. легче заменить трубу, чем
корпус;
- загрязненный, дающий отложения
теплоноситель следует направлять с той стороны поверхности теплообмена, которая
более доступна для очистки (в змеевиках - наружная, в кожухотрубчатых - внутренняя);
- для улучшения теплообмена при
неизменном агрегатном состоянии теплоносителей целесообразно увеличивать
скорость того из них, которому соответствует меньший коэффициент теплоотдачи;
- при конденсации паров необходимо
обеспечивать хороший отвод конденсата с теплообменной поверхности.
5.1 Основные закономерности процесса
теплопередачи
В подавляющем большинстве
теплообменных аппаратов тепло передается от одного теплоносителя к другому
через разделяющую их стенку конвекцией и теплопроводностью (рекуперативные теплообменники).
Количество тепла, передаваемого в единицу времени (тепловая нагрузка аппарата)
определяется из уравнения теплового баланса: Q = Q1×hп = Q2, где hп - коэффициент полезного
использования тепла в аппарате; Q1,
Q2 (Вт) - количество
тепла, отдаваемого одним теплоносителем и воспринимаемого другим (без учета
потерь тепла или холода в окружающую среду через поверхность аппарата, коммуникации
и крепления). При неизменном агрегатном состоянии теплоносителя Qj = Gj×cj×(tjб - tjм),
а при его изменении (кипение, испарение) Qj =
Gj× (ijп - ijк), jÎ(1,2). Здесь Gj - расход теплоносителя
(кг/с), tjб ,tjм - его большая и меньшая
температуры (оС), cj - его удельная
теплоемкость (Дж/(кг*К)) при средней температуре, ijп ,ijк
- теплосодержание пара и конденсата
(Дж/кг) при температуре кипения (конденсации).
Поверхность теплообмена, необходимая
для обеспечения тепловой нагрузки Q,
определяется по формуле: F = Q /(K*Dtср), где K -
усредненный коэффициент теплопередачи (Вт/(м2*К)), Dtср - средняя разность
температур теплоносителей. При их
прямоточном и противоточном движении Dtср = (Dtб - Dtм)/ln(Dtб/Dtм), где Dtб, Dtм - большая и меньшая
разность температур теплоносителей на противоположных концах теплообменной
поверхности. При смешанном и перекрестном движении полученное таким образом
значение Dtср умножается на поправочный
коэффициент et,
значение которого определяется по эмпирическим графическим зависимостям.

Для плоской стенки и труб при отношении их наружного
диаметра к внутреннему dн/d £ 2 коэффициент
теплопередачи определяется по формуле K=(1/a1 + SRi +1/a2)-1,
где
a1, a2 - коэффициенты теплоотдачи от
горячего теплоносителя к стенке и от стенки к холодному (Вт/(м2*K)), SRi
- сумма термических сопротивлений разделяющей стенки, куда входят сопротивления
ее слоев dст i / lст i и слоев загрязнений Rз i = dз i / lз i с обеих сторон стенки (м2×K/Вт). Здесь dст i, dз i - толщина i
- го слоя стенки и загрязнения (м),
lст i, lз i - коэффициенты
теплопроводности их материалов (Вт/(м*К)). Значения dз i, lз i обычно неизвестны, поэтому
значения Rз i либо берутся из справочников, либо их нали-
чие
учитывается умножением значения K,
рассчитанного без учета загрязнений, на коэффициент j (для аппаратов, не требующих частой очистки j=0.7¸0.8; при активном выпадении
осадков из теплоносителей j=0.4 ¸0.5).
Значения коэффициентов теплоотдачи a1, a2 определяются из
критериальных уравнений, форма которых в каждом конкретном случае зависит от
условий теплоотдачи. В эти уравнения чаще всего входят следующие критерии:
Нуссельта Nu = a×l/ l, где
l - определяющий
геометрический размер (м), l - коэффициент
теплопроводности теплоносителя (Вт/(м*K)); Рейнольдса Re = w×l×r/m, где w - скорость течения теплоносителя (м/с), r (кг/м3), m (Па×с) - его плотность и
динамическая вязкость; Прандтля Pr = m×c/ l;
Грасгофа Gr = g×l3×b×Dt/n2, где b - температурный
коэффициент объемного расширения теплоносителя (1/K), Dt - разность его температур у стенки и в ядре потока, n -
кинематическая вязкость (м2/с).
Наиболее часто используемые формы уравнения
теплоотдачи:
1.Теплоотдача при свободном движении теплоносителя (охлаждение
кожухов аппаратов, трубопроводов окружающим воздухом):
Nu = А×(Gr×Pr)n,
где
при Gr×Pr < 500 А = 1.18, n = 0.125;
при 500 £ Gr×Pr <
2×107 А = 0.54, n = 0.25;
при Gr×Pr > 2×107 А = 0.135, n = 0.33.
Определяющая
температура - средняя температура пограничного слоя t = (tст +
tср)/2, где tст, tср - температура стенки и средняя температура теплоносителя.
Определяющий размер - диаметр трубы или высота стенки. В этом случае необходим
учет лучистой составляющей теплового потока, характеризуемый коэффициентом
теплоотдачи лучеиспусканием
aл = 5.67×10-8×e×j×(Tст4 - Tср4)/(
tст - tср),
где
e - степень черноты поверхности (для масляной
краски, окисленной стали
e = 0.75¸0.9), j - коэффициент, зависящий от геометрии
поверхности и условий лучеиспускания, Tст,
Tср - абсолютные температуры.
Общий коэффициент теплоотдачи aо = a + aл.
2.Теплоотдача при вынужденном
движении теплоносителя в трубах и каналах (при отношении длины канала к его
эквивалентному диаметру l/dэ > 50):
турбулентный
режим - Nu = 0.021×Re0.8×Pr0.43×(Pr/Prст)0.25
(Re >10000);
переходный режим - Nu = 0.08×Re0.9×Pr0.43×(Pr/Prст)0.25
(Re = 2300¸10000);
ламинарный
режим - Nu = 0.17×Re0.33×Pr0.43×Gr0.1×(Pr/Prст)0.25
(Re < 2300).
Определяющие
параметры - tср и dэ = 4×S/P, где S, P - площадь поперечного сечения
и пе-риметр канала. При движении теплоносителя в изогнутых трубах (в змеевике)
дополнительная турбулизация потока учитывается умножением правых частей
уравнений на коэффициент eR =
1+3.54×dн/D, где dн, D - наружный диаметр трубы и диаметр ее навивки.
3.Теплоотдача при поперечном (строго
перпендикулярном) омывании теплоносителем пучка труб:
при Re >1000 - Nu = А×Ren×Pr0.33×(Pr/Prст)0.25,
где А = 0.23, n = 0.65 для шахматного расположения труб, А = 0.41, n = 0.6 - для коридорного;
при Re <1000 - Nu = 0.59×Re0.47×Pr0.33×(Pr/Prст)0.25.
При
расчете теплоотдачи в реальных кожухотрубчатых теплообменниках с перегородками
в межтрубном пространстве правые части этих уравнений умножаются на коэффициент
изменения угла атаки ef ~ 0.6. Определяющие
параметры - tср, dн, скорость в самом узком
сечении пучка.
4.Теплоотдача при пленочной
конденсации паров. В этом случае значение коэффициента теплоотдачи определяется
по формуле
, где r - теплота
конденсации пара при заданном давлении
(Дж/кг); rк, lк, mк - плотность, коэффициент
теплопроводности и динамическая вязкость конденсата при температуре конденсации
tк; Dtк = tк -
tст; l - определяющий размер. Для вертикального трубчатого
конденсатора l = H (высота труб), С = 1.15; для горизонтального при подаче
пара в межтрубное пространство l = dн, С = 0.72.
5.Теплоотдача при кипении жидкостей:
при вынужденном движении жидкости в
трубах a = b3×l2× Dtкип2 /(n×s×Tкип), где
b = 0.075 + 0.75×[rп/(rж - rп)], rж, rп - плотности жидкости и
пара; Dtкип = tст - tкип,
tкип- температура кипения жидкости при заданном давлении; Tкип = tкип + 273оС; n, s - кинематическая вязкость и
коэффициент поверхностного натяжения жидкости (Н/м);
при пузырьковом кипении на наружной
поверхности пучков труб a=600×j×p1.33×Dtкип2.33, где j - экспериментально
определяемый коэффициент (для воды j=1), р - давление в аппарате (МПа).
Расчет теплоотдачи для
случая однослойной стенки сводится к решению системы, содержащей уравнения
теплоотдачи (по обеим сторонам стенки) и уравнения теплового баланса: a1×(t1 - tст1) = a2×(tст2
- t2),
a1×(t1 - tст1) [или a2×(tст2 - t2)] = (tст1
- tст2)×lст/dст,
где
tст1, tст2, t1,
t2 - температуры стенки со
стороны теплоносителей и средние температуры теплоносителей. Система
дополняется соответствующими критериальными уравнениями. Решение этой системы -
значения a1,a2, tст1, tст2.
Ориентировочные значения
коэффициентов теплоотдачи, Вт/(м2*K):
- турбулентное течение воды в трубах 1000 - 5500
- турбулентное течение воды снаружи
труб 3000 - 10000
- турбулентное движение газов в трубах 50 - 150
- турбулентное движение газов снаружи
труб 100 - 300
- ламинарное течение воды в трубах 300 - 430
- ламинарное движение газов в трубах 10 - 20
- свободная конвекция воды 300 - 900
- свободная конвекция газов 3 - 10
- кипение воды 2000 - 24000
- конденсация водяного пара 900 - 15000
- кипение органических жидкостей 300
- 3500
- конденсация паров органических
жидкостей 230 - 3000
5.2 Кожухотрубчатые теплообменники
Это самая распространенная
конструкция теплообменной аппаратуры в химической промышленности (около 80%
всех теплообменников - кожухотрубчатые). Они достаточно просты в изготовлении,
надежны в эксплуатации и универсальны, т.е. могут быть использованы для осуществления
теплообмена между жидкостями, парами, газами в любом сочетании в широком
диапазоне давлений и температур.
Поверхность теплобмена кожухотрубчатых теплообменников F = p×dср×l×n, где l - длина труб, n - их
число, dср= (dн + d)/2 - средний диаметр. Наиболее популярны трубы с наружным
диаметром 20 и 25 мм, толщиной стенки 2 мм. С увеличением длины труб и уменьшением
диаметра кожуха стоимость теплообменника снижается (наиболее дешевы аппараты с
длиной труб 5¸7 м).
Приемлемые значения коэффициентов
теплоотдачи в этих аппаратах обеспечиваются при движении жидких теплоносителей
со скоростями w ³ 1.5 м/с, а газообразных - с
w = 8¸30 м/с. Для увеличения
скорости движения теплоносителей в трубах кожухотрубчатые теплообменники
комплектуются распределительной камерой с продольными перегородками,
обеспечивающими несколько (2, 4, 6) ходов по трубному пространству. Поскольку
интенсивность теплоотдачи при поперечном обтекании труб выше, чем при
продольном, в межтрубном пространстве устанавливаются поперечные перегородки,
обеспечивающие зигзагообразное движение теплоносителя.
Параметры кожухотрубчатых теплообменников
Тип
|
|
|
|
|
|
Обозначение
|
Н, ТН
|
К, ТК
|
П, ТП
|
У, ТУ
|
ПК
|
Доля,
%
|
75
|
15
|
3
|
7
|
F, кв. м
|
1 - 5000
|
1 - 5000
|
10 - 1250
|
10 - 1400
|
170 - 1900
|
D, м
|
0,16 - 3,0
|
0,16 - 3,0
|
0,32 - 2,8
|
0,32 - 2,8
|
0,8 - 1,8
|
L, м
|
1 - 9
|
1 - 9
|
3 - 9
|
3 - 9
|
6 - 9
|
Fуд, кв. м/ куб.м
|
35 - 75
|
P, атм.
|
40
|
25
|
64
|
64
|
64
|
T, oС
|
-30
¸ +350
|
-30
¸ +350
|
+30
¸ +450
|
-30
¸ +350
|
-30
¸ +350
|
DT, oС
|
30
|
80
|
>100
|
100
|
>100
|
Рабочая
среда в трубном пространстве
|
Жидкость,
пар, газ, загрязненные, коррозионно-активные, при высоких давлениях и
температурах, при меньших расходах.
|
Рабочая
среда в межтрубном пространстве
|
Чистые
жидкости, газы и пары при низком давлении, конденсирующиеся пары, кипящие
жидкости.
|
F - площадь поверхности теплообмена D - Диаметр кожуха
L - Длина рабочей части Fуд - Удельная поверхность
теплообмена
P - Допустимое давление T - Температурный диапазон
DT - Допустимый
перепад температур
В аппаратах типа Н и К трубы в трубных
решетках размещают только по вершинам равносторонних треугольников
("шахматное"), а в остальных возможно размещение и по вершинам
квадратов ("коридорное"), см. рис 5.1. Шахматное расположение труб
более компактно, а при коридорном возможна механическая очистка их внешней
поверхности. Величина шага t между
трубами зависит от их диаметра: при dн
= 20 мм
t = 26 мм, при dн = 25 мм t =
32 мм.
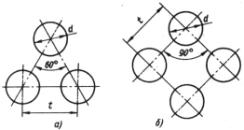
Рис. 5.1
Размещение труб в
трубных решетках
а)"шахматное",
б)"коридорное".
5.2.1 Теплообменники типа Н
Особенностью аппаратов типа Н
(рис. 5.2) является жесткое соединение труб с трубными решетками и решеток с
кожухом (сваркой). В них исключается возможность взаимного перемещения труб и
кожуха,
поэтому их еще называют теплообменниками жесткой конструкции. Для уменьшения
количества теплоносителя, проходящего между
трубным пучком и кожухом
(минующего основную поверхность теплообмена), в этом пространстве размещают
специальные заполнители: продольные полосы, приваренные к стенке кожуха, или
глухие трубы (рис. 5.3). Отбойник (круглая или прямоугольная пластина на входе
в межтрубное пространство), защищает трубы от местного эрозионного изнашивания.
Чаще всего трубы крепят в трубной решетке развальцовкой - обкаткой изнутри
специальным роликовым инструментом. Начальный зазор между трубой и отверстием
обычно равен 0.25 мм (потеря пластичности металла после развальцовки и
опасность
растрескивания тем меньше, чем меньше зазор).
Для обеспечения качественной развальцовки и возможности замены труб материал решетки
должен быть тверже материала труб. Высота выступа трубы над решеткой обычно
равна толщине трубы. При давлениях до 0.6 Мпа применяют развальцовку в гладких
отверстиях (иногда с отбортовкой выступа) , см. рис. 5.4а. Прочность и герметичность
соединения значительно возрастают при развальцовке в отверстиях с канавками
глубиной 0.5 мм (рис. 5.4б). Трубы развальцовывают на глубину 1.5×
dн или на всю толщину
решетки, если она меньше 1.5× dн
(со стороны межтрубного пространства оставляют поясок шириной 3 мм, чтобы не
подрезать трубу). Для исключения коррозии по причине проникновения среды между
трубой и толстой решеткой развальцовку выполняют двумя поясками: шириной 1.5×
dн со стороны
распределительной камеры и 0.75× dн
со стороны межтрубного пространства. При креплении труб в решетке сваркой с развальцовкой
(рис. 5.4в) вначале выполняют сварку. Пайку концов труб в решетках (рис. 5.4г)
применяют при изготовлении теплообменников из меди и ее сплавов.
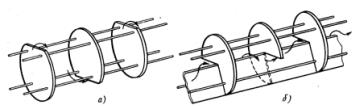
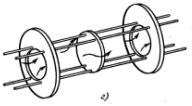
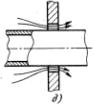
Рис.
5.5 Поперечные перегородки в межтрубном
пространстве
а) сегментные; б) секторные; в) кольцо-диск;
г) сплошные (для чистых жидкостей)
Поперечные перегородки в межтрубном пространстве (рис. 5.5) не только
обеспечивают движение теплоносителя в направлении, перпендикулярном оси труб, и
увеличение его скорости, но и выполняют роль опор трубного пучка, обеспечивая
неизменность расстояния между трубами. Они также уменьшают вибрацию труб,
которая представляет серьезную опасность в случаях, когда по межтрубному
пространству с большой скоростью движется газ.
Наиболее широко на практике
применяют сегментные перегородки, см. рис. 5.5а. Высота удаляемого сегмента -
примерно 1/3 диаметра кожуха D,
расстояние между перегородками - около 0.5×D. Утечки
теплоносителя в зазорах между перегородками и кожухом ухудшают условия
теплообмена, поэтому величина зазора ограничивается (при D £ 600 мм он не должен
превышать 1.5 мм). Толщина продольных перегородок распределительных камер и
крышек не должна быть меньше 6 мм.
Теплообменники типа Н просты по
устройству и сравнительно дешевы, но имеют два крупных недостатка: 1) наружная
поверхность труб недоступна для механической очистки; 2) область их применения
ограничена разностью температур теплоносителей 50о С по причине
возникновения в кожухе и трубах так называемых температурных напряжений (при
разных температурах стенок труб и кожуха их температурные деформации
неодинаковы). Для уменьшения температурных напряжений при пуске аппаратов типа
Н рекомендуют сначала заполнять межтрубное пространство (для выравнивания
температур кожуха и труб). Если расчетная разность температур кожуха и труб превы-
шает 30о С, рекомендуется использовать теплообменники с
частичной (тип К, ПК) или полной компенсацией температурных напряжений (тип
П,У).
5.2.2 Теплообменники с компенсацией
температурных напряжений
Между двумя частями кожуха теплообменников
типа
К вваривают линзовый компенсатор с обтекателем, уменьшающим гидравлическое
сопротивление межтрубного пространства. Одно- и многоэлементные линзовые
компенсаторы (рис. 5.5а,б) изготавливают обкаткой коротких цилиндрических
обечаек. Компенсирующая способность с ростом числа элементов увеличивается, однако
применять компенсаторы с числом линз более 4-х не рекомендуется, т.к. резко
снижается сопротивление ко
жуха изгибу. В нижней части компенсаторов горизонтальных аппаратов
имеются дренажные отверстия с заглушками для слива затекающего за обтекатель теплоносителя.
Кроме линзовых, в аппаратах типа К
используют следующие компенсаторы, см. рис. 5.6в,г,д,е: сваренные из двух
полулинз, полученных из листа штамповкой; из плоских колец, соединенных
пластиной; сваренные из двух полусферических элементов; тороидальные, изготовленные
из согнутой трубы с вырезанной внутренней поверхностью. Эти компенсаторы
дешевле линзовых, но из-за наличия сварных швов не могут выдерживать больших
напряжений.
К аппаратам, обеспечивающим
частичную компенсацию температурных деформаций за счет гибких элементов
относится также теплообменник с расширителем на кожухе (рис 5.7).
Дополнительное преимущество этой конструкции - исключение застойных зон в
межтрубном пространстве вблизи трубных решеток, которые возникают из-за
расположения штуцеров ввода и вывода теплоносителя на некотором расстоянии от
решеток. Расширитель играет роль компенсатора, а распределитель направляет поток
теплоносителя к трубной решетке. Теплообменники с компенсаторами и
расширителями дороже аппаратов типа Н, но допускают гораздо больший перепад
температур стенок труб и кожуха. Область их применения ограничена давлением теплоносителей
2.5 МПа.
В кожухотрубчатых
теплообменниках типа П (с плавающей головкой)
температурные деформации кожуха и труб практически исключены, т.к. только одна
трубная решетка приварена к корпусу, а другая имеет возможность свободного
осевого перемещения, см. рис. 5.8. Подвижная трубная решетка вместе с присоединенной
к ней крышкой образует "плавающую головку", которая перемещается внутри
кожуха при нагревании и удлинении труб. Однако компенсация температурных деформаций
в аппаратах типа П не является полной, т.к. различие температурных расширений
труб может привести к короблению трубной решетки. Поэтому в многоходовых теплообменниках
типа П с диаметром кожуха D > 1 м
при значительном (>100о С) изменении температуры среды в трубном
пучке устанавливают разрезные по диаметру плавающие головки. Недостаток этих аппаратов
по сравнению с теплообменниками типа Н и К - больший зазор между кожухом
и трубами (на ширину фланца плавающей головки), достоинство - возможность извлечения
трубного пучка из кожуха и механической очистки внешней
поверхности труб при их коридорном расположении. Крепление плавающей головки
к решетке разрезным фланцем, который состоит из двух полуколец, стянутых ограничительным
кольцом (рис. 5.9), позволяет легко извлекать трубный пучок из кожуха при минимальном
зазоре.
Конструкция теплообменника типа
ПК (с плавающей головкой и компенсатором) отличается от рассмотренной
наличием на одной из крышек удлиненного штуцера, внутри которого размещен линзовый
компенсатор, соединенный с плавающей головкой (рис. 5.10). Теплообменники этого
типа выполняют одноходовыми с противоточным движением теплоносителей и
используют при повышенных давлениях сред (5¸10 МПа). Компенсаторы
отличаются от используемых в аппаратах типа К меньшими диаметрами, большим
числом линз, меньшей толщиной стенки. Теплообменники типа ПК можно использовать
при перепаде давлений не более 2.5 МПа, поэтому подача теплоносителей в трубное
и межтрубное пространство осуществляется одновременно.
В кожухотрубчатых теплообменниках типа У (с U-образными трубами),
см. рис. 5.11, обеспечивается свободное удлинение труб и полностью отсутствуют
тем
пературные напряжения. Еще одно преимущество этой конструкции -
возможность периодического извлечения трубного пучка из кожуха для очистки.
Теплообменники типа У являются двухходовыми по трубному пространству и одно-
или двухходовыми по межтрубному. В последнем случае в межтрубном пространстве
устанавливается продольная перегородка, извлекаемая из кожуха вместе с трубами.
Разность температур стенок труб по ходам не должна превышать 100о С,
в противном случае могут возникнуть опасные напряжения в трубной решетке. Поскольку
механическая очистка внутренней поверхности U-образных труб практически невозможна,
в трубное пространство этих аппаратов направляют среды, не образующие твердых отложений.
Чистка внутренней поверхности труб осуществляется подачей водяного пара, горячих
нефтепродуктов, химических реагентов, потока воды с абразивным материалом.
Аппараты типа У не нашли широкого применения по причине относительно плохого заполнения
кожуха трубами из-за ограничений на радиус их изгиба (³ 4× dн), а также сложности размещения труб и отсутствия
возможности их замены (за исключением внешних).
5.2.3 Расчеты кожухотрубчатых теплообменников
К числу технологических расчетов
кожухотрубчатых теплообменников относятся тепловой и гидравлический расчет. Методика
теплового расчета достаточно подробно рассматривалась в курсах "Термодинамика"
и "Процессы и аппараты химической технологии". Целью гидравлического
расчета является определение гидравлических сопротивлений его трубного и
межтрубного пространства, определение мощности насосов и газодувок, используемых
для транспортировки теплоносителей через аппарат.
Без учета неизотермичности потока общее
сопротивление трубного пространства (рис. 5.12)
Dрт = Dр1 + z×(Dр2 + Dртт + Dр3) + Dр4 + {Dр5},
межтрубного
Dрм = Dр6 + (l/lп)×Dртм + (l/lп - 1)×Dр7 + Dр8.
Здесь учтены следующие потери давления: Dр1, Dр4 - при входе и выходе потока из распределительной
камеры; Dр2, Dр3 - при входе и выходе потока из труб; Dр6, Dр8 - при входе и выходе потока из межтрубного пространства; Dртт, Dртм - на трение в трубах и межтрубном пространстве; Dр5 - при повороте труб на 180о
(в аппаратах типа У); Dр7 - на
огибание потоком перегородки. В этих формулах z - число ходов теплоносителя по трубам, l - длина труб, lп -
расстояние между перегородками.
Потери давления в местных сопротивлениях Dрi = zi×(r×wi2/2), i = 1,...,8, где r -
плотность теплоносителя, wi - скорость
потока в узком сечении рассматриваемого участка (ориентировочное значение условного
прохода штуцера dш =
0.3×D 0.86), zi
- коэффициент местного сопротивления (даются в справочниках). Потери на трение:
- Dртт
= lт×(l/d)×(r×wт2/2), где wт
- скорость потока в трубах, lт
- коэффициент трения в трубах (64/Reт
при Reт £ 2300
и 0.316/Reт0.25
при 2300< Reт <100000);
- Dртм
= lм×(r×wм2/2), где wм
- скорость потока в узком сечении межтрубного пространства, lм
- коэффициент трения в межтрубном пространстве ((4+2.31×D/dн)/Reм0.28 для "шахматного" расположения
труб и (5.4+1.054×D/dн)/Reм0.28 - для "коридорного").
Коэффициенты местных
сопротивлений кожухотрубчатого теплообменника
Вход в распределительную камеру - 1
Поворот потока и вход в трубы - 1
Выход из труб и поворот потока - 1,5
Выход из распределительной камеры - 0,5
Поворот в U-образных
трубах -
0,5
Вход в межтрубное пространство - 1,5
Огибание перегородок в межтрубном пространстве - 1,5
Выход из межтрубного пространства - 1,5
Мощность,
затрачиваемая на преодоление сопротивления трубного или межтрубного
пространства (Dp) N
= V×Dp/h, где V - объемный расход теплоносителя, h - к.п.д. машины,
создающей напор.
Методика механических расчетов
кожухотрубчатых теплообменников регламентирована ОСТ 26.1185-81. Сюда входят расчеты
кожуха и труб на прочность и устойчивость, определение необходимой толщины
трубной решетки, толщины стенки и числа линз компенсатора, проверка условия
прочности кожуха в месте присоединения решетки, а также условия прочности
крепления труб. Рассмотрим упрощенный вариант этой методики применительно к
теплообменникам типа Н и К.
В расчетах будем учитывать только осевые деформации кожуха и
труб, вызванные разностью их температур и разностью давлений в трубном и
межтрубном пространстве. Предположим, что трубная решетка не деформируется, температура
кожуха tк равномерно распре
делена по его длине и сечению, а температура труб постоянна и равна tт.
В
этом случае осевые деформации кожуха и труб определяются по формулам (рис.
5.13):
- под действием разности температур Dкt = bк×(tк - t0)×l,
Dтt = bт×(tт - t0)×l, где bк, bт - температурные
коэффициенты линейного расширения кожуха и труб (1/K), t0-
температура их изготовления(оС);
- под действием разности давлений Dтр=m×(рт- рм)×(d + sт)×l/(Eт×sт),
Dкр = m×рм×(D + sк)×l/(Eк×sк), где m - коэффициент Пуассона (для
металлов m ~ 0.3), рт, рм -
давление в трубном и межтрубном пространстве,
sт, sк - толщина стенки труб и кожуха,
Ет, Ек - модуль упругости материала труб и кожуха.
Условие совместимости деформаций при одновременном действии разности
температур и давлений: Dкt + Dкp + Dк¢ = Dтt + Dтp + Dт¢, (5.1)
где
Dк¢= Nк×l/(Eк×sк), Dт¢= Nт×l/(Eт×sт), Nк, Nт - осевые силы, действующие на единицу длины окружности кожуха и
трубы (Н/м). Условие равновесия трубной решетки:
p×(D + sк)× Nк + p×n×(d + sт)× Nт - Qт + Qм = 0, (5.2)
где
n - число труб в теплообменнике, Qт = n× рт×p×d2/4, Qм = рм×p×(D2 - n×dн2)/4 - силы, действующие на
трубную решетку со стороны распределительной камеры и межтрубного пространства.
Решив систему уравнений (5.1), (5.2) и получив значения Nк и Nт
(положительная соответствует растяжению, отрицательная - сжатию), определим
окружные напряжения в кожухе и трубах и сравним с допускаемыми для их
материалов, т.е. проверим выполнение условий прочности кожуха sк = |Nк|/sк < [s]к и труб sт = |Nт|/sт < [s]т.
При Nт < 0 проверяется выполнение условия устойчивости (сохранения
формы сечения) для труб |Nт|/(sт×j) < [s]т, где j ~ 0.4 - коэффициент уменьшения
допускаемого напряжения при продольном изгибе. Кожух проверяют на устойчивость
при Nк< 0 (по ГОСТ
14249-89):
, где [F]n = p×(D + sк)× sк× [s]к,
[F]e = 0.031×Eк×D×sк/nу
-
допускаемые сжимающие усилия из условий прочности и устойчивости соответственно,
nу- коэффициент запаса
(для рабочих условий 2.4, для испытаний 1.8).
Толщина трубной решетки sр кожухотрубчатого
теплообменника типа Н или К должна обеспечивать выполнение условия ее прочности
при совместном действии на нее осевых сил Nк
и Nт. Кроме того, она
должна обеспечивать возможность крепления труб в решетке: для аппаратов типа Н
, типа К -
. Здесь [s]р - допускаемое
напряжение для материала решетки; jр =1 - dн/h - коэффициент ее ослабления
отверстиями под трубы с шагом h;
с - конструктивная прибавка
(1¸3 мм); Kл
= 1 + (рм/рт)×(1 - bл2)/ bл2 + 4×Рл/(p×D2×рт),
bл = dл/Dл - отношение внутреннего диаметра линзы к наружному,
Рл = |bт×(tт - t0) - bк×(tк - t0)|×l×Eл/М -
усилие в компенсаторе, М = nл×0.06×(1 - bл)×D2/(p×sл3), Ел - модуль упругости материала компенсатора,
- толщина стенки компенсатора,
sлт - предел текучести его
материала при 20 оС, nл
- число
линз
в компенсаторе. Для определения одного из трех параметров компенсатора
(bл, sл, nл)
при двух заданных используется равенство Pл
= p×(D + sк)× |Nк|.
Условием прочности крепления труб в решетке является
выражение Fт
£
[Fт], где Fт
= p×(d + sт)× Nт - усилие в соединении трубы с решеткой, [Fт] - допускаемое усилие:
-
при развальцовке труб [Fт] = p×(d + sт)×lв×[q];
- при сварке [Fт]
= 0.3× p×(d + sт)×d×min{[s]т,[s]р};
- при развальцовке со сваркой [Fт] = (d + sт)×lв×[q] + 0.57×(d + sт)×d×min{[s]т,[s]р}.
Здесь lв- глубина
развальцовки труб, d - высота сварного шва, [q] - допускаемая удель-
ная
нагрузка на единицу площади соединения развальцовкой (для гладких отверстий -
14.7 МПа, в канавки - 29.4 МПа, с отбортовкой - 39.2 МПа).
5.3 Пленочные испарители
Пленочные испарители предназначены
для реализации процесса кипения жидкостей в тонкой пленке, что существенно
повышает интенсивность теплоотдачи и практически полностью устраняет гидростатическую
депрессию (повышение температуры кипения жидкости за счет гидростатического
давления ее столба по мере стекания вниз по вертикальным трубам). Эти аппараты
могут применяться для отгонки из жидкостей легколетучих компонентов при
вакуумной ректификации, концентрирования термолабильных (неустойчивых к действию
повышенных температур) и кристаллизующихся растворов, для проведения химических
реакций в системах газ-жидкость.
Наиболее распространенная
конструкция пленочного испарителя - кожухотрубчатый со стекающей пленкой
(рис. 5.14). Это вертикальный прямоточный теплообменник, в верхней части каждой
трубы которого установлено оросительное устройство. Жидкость подается на
верхнюю трубную решетку, равномерно распределяется по трубам и в виде пленки,
образованной оросителем, стекает по внутренней поверхности труб. Частичное
испарение жидкости происходит за счет подачи в межтрубное пространство
насыщенного водя
ного пара давлением до 1.3 МПа или пара ВОТ давлением до 1.06 МПа.
Образовавшаяся в трубах парожидкостная смесь после выхода из аппарата поступает
на сепарацию.
Режим устойчивого пленочного течения
жидкости выбирается из следующих соображений:
-
минимально необходимая для полного смачивания всей внутренней
поверхности труб плотность орошения
м2/с, где nж, rж - кинематическая вязкость и
плотность испаряемой жидкости, s - ее поверхностное
натяжение на границе с паром;
-
по мере стекания пленки происходит испарение части жидкости и унос капель
с ее поверхности потоком пара, поэтому плотность орошения будет наименьшей на
нижнем участке труб: Гн = Gк×(1-У)/(rж×П) > Гmin,
где Gк - расход жидкости,
упаренной до конечной концентрации хк,
П = p×d×n - полный смоченный периметр
труб аппарата при их числе n и
внутреннем диаметре d, У - унос жидкости,
т.е. отношение массового расхода жидкости, находящейся в паровом потоке к ее
полному расходу (скорость пара в трубах следует подбирать так, чтобы
выполнялось условие У < 0.3);
-
для термолабильных растворов среднее время пребывания жидкости в пленке
tср = Vж×rж/Gср не должно превышать предельно допустимого времени
их упаривания tдоп = 10Dh/p, где Gср = (Gн + (1-У)×Gк)/2 - средний расход
жидкости в стекающей пленке, Gн -
расход жидкости с начальной концентрацией хн
(Gн×хн = Gк×хк), Vж=F×d - объем жидкости, находящейся на теплообменной
поверхности аппарата F, Dh - показатель опасности термического
разложения жидкости, р - давление в
аппарате, d - средняя толщина стекающей
пленки, определяемая значением критерия Рейнольдса
:
при
Reпл £ 1200 d = (0.75×Reпл×nж2/g)0.33, а при Reпл
>1200 d = 0.21× (nж2/g)0.33×Reпл0.533.
При выполнении теплового расчета кожухотрубчатый
испаритель со стекающей пленкой рассматривается как аппарат идеального
вытеснения с разграниченными зонами нагревания и испарения жидкости. Расчет
теплопередающих поверхностей каждой зоны проводится раздельно, причем расчет
зоны испарения дополняется определением значения теплового потока q, обеспечивающего теплообмен без
разрушения пленки пузырьками образующегося пара:
, где
сж, lж - удельная теплоемкость и
теплопроводность жидкости, rп - плотность образующегося
пара, rи - удельная
теплота парообразования, Ткип-
абсолютная температура кипения жидкости, a - коэффициент теплоотдачи
от стенки трубы к свободно стекающей пленке жидкости, который при Pr = 4¸300 практически не зависит
от режима течения и может быть определен по формуле
.
В последние годы получили
распространение роторные пленочные испарители, в
которых отсутствуют трубы, а пленка жидкости, стекающая по внутренней
поверхности кожуха, подвергается механическому перемешиванию. Перемешивание
пленки существенно интенсифициует как процесс теплообмена между жидкостью в
пленке и стенкой аппарата, так и массообмена между жидкостью и газом.
К достоинствам этих аппаратов можно также отнести повышение устойчивости
пленки за счет создаваемой ротором центробежной силы и незначительное время
пребывания жидкости в аппарате (важно для термолабильных веществ).
Наиболее популярны аппараты с
шарнирно закрепленными лопастями, (рис. 5.15). Лопасти изготавливаются из
коррозионно-стой-ких сталей, а их трущиеся кромки защищаются накладками из
бронзы или фторопласта. При предварительном выборе такого аппарата учитываются
следующие рекомендации:
-
аппарат, используемый в качестве химического реактора должен иметь
поверхность теплообмена
,где tр - продолжительность
реакции,
l = p×D/z, z-
число лопастей в горизонтальном сечении аппарата;
-
при обработке термолабильных растворов его теплообменная поверхность
должна удовлетворять условию
.
К недостаткам роторных испарителей
по сравнению с кожухотрубчатыми можно отнести малую поверхность теплообмена,
усложнение и удорожание конструкции. Отметим также трудности обеспечения
одинаковых зазоров между лопастями и стенкой аппарата.
5.4 Другие конструкции теплообменников
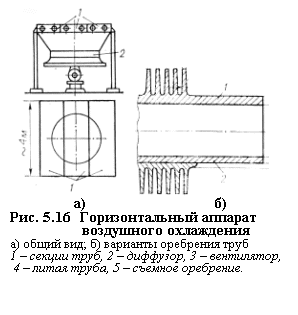
Аппараты воздушного охлаждения находят
применение в химической и нефтехимической промышленности в качестве холодильников-конденсаторов.
Их преимущества перед аппаратами водяного охлаждения: отсутствует оборудование
для подготовки и перекачки воды, снижается трудоемкость и стоимость ремонтных
работ, не требуется специальной очистки наружной поверхности труб, облегчается
регулирование процесса охлаждения.
Поверхность теплообмена
горизонтального аппарата воздушного охлаждения, см. рис. 5.16, образована
наружной поверхностью оребренных труб, собранных в секции. Воздух, нагнетаемый
вентилятором, омывая трубы, обеспечивает охлаждение или конденсацию проходящей
по ним среды. При повышенной температуре окружающего воздуха автоматически
включаются форсунки, распыливающие в потоке воздуха воду, при пониженной - отключается
вентилятор. Интенсивность теплоотдачи можно регулировать, изменяя расход воздуха
путем поворота лопастей вентилятора или установки поворотных жалюзийных заслонок
над секциями труб.
Теплообменники типа "труба
в трубе" используются для нагревания или охлаждения в системах
жидкость-жидкость, когда расходы теплоносителей невелики и они не
меняют
агрегатного состояния. При равных теплообменных характеристиках эти аппараты
имеют меньшее гидравлическое сопротивление, чем кожухотрубчатые, но менее
компактны и более металлоемки.
Наиболее распространенный
теплообменник "труба в трубе", см. рис. 5.17, состоит из отдельных
звеньев, включающих наружную (кожуховую) и внутреннюю (теплообменную) трубу.
Соединяя внутренние трубы коленами, а наружные - штуцерами, звенья собирают в вертикальные
секции. При разности температур теплоносителей более 70 оС и
необходимости механической очистки межтрубного пространства применяют
теплообменники с сальниками на наружных трубах.
Оросительные теплообменники (рис.
5.18) состоят из нескольких рядов труб, расположенных одна над другой и соединенных
коленами. По наружной поверхности труб стекает вода, а внутри прокачивается
охлаждаемая среда. Для распределения воды над верхней трубой (а при большом
числе труб и между ними) устанавливаются трубчатые или желобковые оросители.
Расход воды в этих аппаратах меньше, чем в теплообменниках других типов, т.к.
тепло от жидкости в трубах отводится не только за счет нагрева орошающей воды,
но и частичного ее испарения. Оросительные теплообменники малоэффективны, но просты
в изготовлении и ремонте. Чаще всего они устанавливаются вне зданий и используются
для охлаждения агрессивных сред (серной кислоты).
Основным материалом для изготовления
блочных теплообменников является графит, пропитанный
фенолформальдегидной смолой. Эти аппараты собираются из отдельных блоков,
имеющих сквозные горизонтальные и вертикальные каналы круглого сечения (рис.
5.19). Боковые переливные камеры соединяют горизонтальные каналы различных блоков.
Соединения блоков уплотняются прокладками из фторопласта.
Блочные графитовые
теплообменники весьма эффективны, т.к. графит стоек к воздействию агрессивных
сред (кислот, щелочей, органических растворителей), а по теплопроводности в 4¸6 раз превосходит коррозионно-стойкую
сталь. Недостаток - невысокая прочность (хрупкость).
В спиральных теплообменниках
поверхность теплообмена образована двумя
стальными лентами толщиной 3¸6 мм и шириной 400¸1250 мм, свернутыми в
спираль. Внутренние концы лент приварены к глухой перегородке, а наружные -
друг к другу. С торцов аппарат закрыт плоскими крышками, установленными на
прокладках (рис. 5.20). В результате образуются два изолированных друг от друга
спиральных канала толщиной 2-8 мм, в которые направляются теплоосители (обычно
противоточно).
Стандартные спиральные
теплообменники имеют поверхность теплообмена 10¸100 м2, применяются
при давлениях до 1 МПа и температурах 20¸200 оС в
качестве нагревателей и охладителей жидкостей и га
зов, конденсаторов паров. Благодаря простоте изготовления,
компактности, малому гидравлическому сопротивлению, возможности работы с загрязненными
жидкостями доля этих теплообменников в химической и смежных отраслях
промышленности в последние годы увеличивается.
Те же достоинства характерны и
для пластинчатых теплообменников, популярность которых в последнее
время также растет. Кроме того, они отличаются высокой интенсивностью
теплообмена, удобством монтажа, высоким коэффициентом унификации. Пластинчатый
теплообменник (рис. 5.21) состоит из ряда пластин, размещенных на горизонтальных
штангах между неподвижной и нажимной плитами.
Пластины штампуют из
листовой стали толщиной 0.7¸1 мм. Они имеют четыре
проходных отвестия, образующих благодаря конструкции разделяющих их резиновых
прокладок две изолированные системы каналов. Для увеличения поверхности теплообмена
и турбулизации потока теплоносителя поверхность
пластин выполняют гофрированной или ребристой. С учетом свойств
резиновых прокладок температура теплоносителей ограничивается 150 оС,
давление не должно превышать 1 МПа.