|
14
14. Колонные массообменные аппараты
Тарельчатые колонны.
В зависимости от способа организации контакта фаз колонные аппараты подразделяют на тарельчатые, насадочные и пленочные, а в зависимости от рабочего давления - на работающие под давлением, атмосферные и вакуумные. Около 60 % используемых в России аппаратов для абсорбции и ректификации представляют собой тарельчатые колонны, остальные - насадочные колонны. Последние при правильной организации гидродинамики процесса часто более экономичны, чем тарельчатые.
Из-за сложности изготовления и высокой стоимости пленочные аппараты мало используют в промышленности.
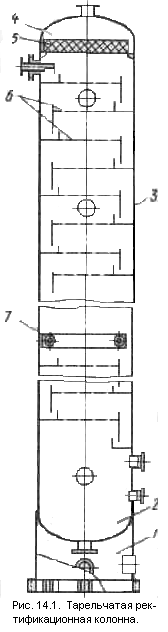
|
Тарельчатые колонные аппараты (рис. 14.1) состоят, как правило, из вертикального корпуса 3, сферической или эллиптической крышки 4, днища 2 и жестко скрепленной с корпусом опорной обечайки 1 цилиндрической или конической формы. Использование конических опор для высоких колонн небольшого диаметра способствует повышению их устойчивости и уменьшению нагрузки на опорную поверхность фундаментного кольца. Внутри корпуса колонны смонтированы тарелки 6, устройство 7 для ввода сырья, отбойное устройство 5 и штуцера для жидкости и пара.
Для удобства монтажа и ремонта тарелок расстояние между ними желательно принимать не менее 450 мм. Монтаж и обслуживание тарелок в аппаратах с цельносварным корпусом выполняют через люки. Люки на корпусе колонны рекомендуется располагать через каждые пять-десять тарелок в зависимости от диаметра аппарата и типа контактных устройств. Диаметр люков может колебаться от 450 до 600 мм, а расстояние между тарелками в месте установки люка от 800 до 1000 мм. Корпуса тарельчатых колонных аппаратов изготовляют большей частью с постоянным по высоте диаметром, хотя для колонн больших размеров в случае, если нагрузка по жидкости и пару (газу) значительно изменяется по высоте колонны, корпус может быть выполнен ступенчатым, т. е. состоящим из частей разного диаметра, соединенных конусными переходами.
На корпусе, например, ректификационной колонны предусматривают штуцера: ввода продукта и вывода пара, ввода флегмы и пара из кипятильника, вывода кубового остатка и циркулирующей кубовой жидкости в кипятильник.
|
Кроме того, аппарат снабжают штуцерами для измерения давления и температуры по высоте аппарата, уровня жидкости, отбора проб и др.
Места ввода сырья и вывода промежуточных фракций зависят от состава сырья; поэтому предусматривают несколько запасных штуцеров по высоте колонны.
Корпус тарельчатой колонны может быть выполнен либо сварным, либо состоящим из царг.
Корпуса аппаратов, работающих при больших рабочих давлениях, а также аппаратов диаметром более 1200 мм выполняют цельносварными. Аппараты диаметром 400-1000 мм изготовляют в царговом исполнении, если рабочее давление в них не превышает 1,6 МПа.
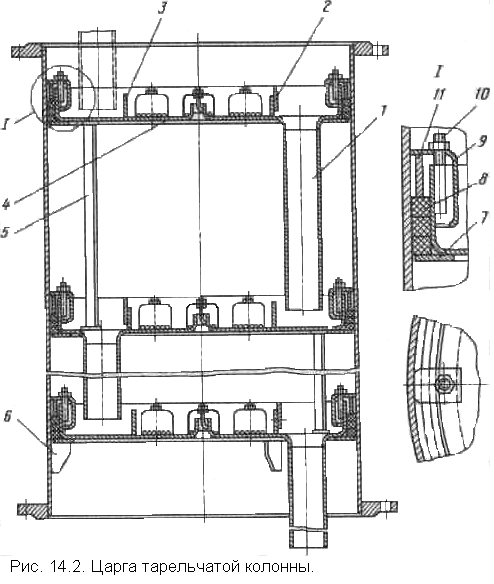
|
Аппараты в царговом исполнении снабжают неразъемными тарелками (рис. 14.2), представляющими собой отбортованный металлический диск с устройствами (отверстия, клапаны, колпачки) для ввода пара (газа) на тарелку и слива жидкости. Для создания необходимого уровня жидкости на тарелке 4 установлены сливная 2 и переливная 3 перегородки. Высота переливной перегородки постоянна; она образует так называемый переливной карман, в который погружена сливная труба 1 расположенной выше тарелки. Высоту сливной перегородки можно регулировать для поддержания необходимого уровня жидкости на тарелке.
|
Нижняя тарелка в царге установлена на кронштейнах 6, а остальные - на стойках 5. Упорные кольца 7 предназначены для герметизации тарелок. В зазоре между тарелкой и корпусом колонны установлены прокладки 8 из асбестового шнура, закрепленные нажимным кольцом 11, скобами 9 и шпильками 10. В аппаратах диаметром 1200 мм и более используют тарелки разборной конструкции. Они состоят из отдельных секций 4, которые крепятся к опорной раме 1 (рис. 14.3) струбцинами 2, винтами 3 и прижимными планками 5. Опорная рама приварена к корпусу колонны. Герметичность соединений секций тарелки с опорной конструкцией обеспечивают прокладки 5.
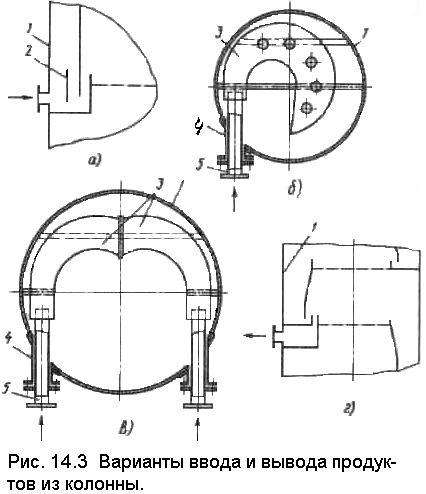
|
Конструкция узла ввода сырья в колонну зависит от фазового состояния поступающей смеси. Жидкое питание, а также орошающая жидкость (флегма), вводятся непосредственно в переливные карманы тарелок. Переливные карманы, в которые вводится жидкость, обычно углублены ниже тарелки примерно на 300 мм. Иногда для гашения энергии струи в переливном кармане устанавливают отражательную пластину. При подаче сырья в парожидкостном состоянии энергия струи может быть весьма большой и вызывает изнашивание корпуса 1 колонны. |
Для защиты корпуса аппарата от эрозионного воздействия струи сырье подается через специальное устройство - улиту. Форма улиты должна обеспечивать равномерное распределение пара по сечению аппарата. На рис. 14.3, б показана конструкция улиты для ввода сырья одним потоком, на рис. 14.3, в - двумя потоками. В этих конструкциях улита 3 крепится к корпусу колонны 1. Штуцера 4 ввода сырья в колонну быстро изнашиваются, поэтому их защищают гильзой 5, замена которой при ремонте колонны не сложна.
В колонне с боковыми выводами, предназначенной для разделения смеси на несколько компонентов, вывод жидкости из колонны осуществляется так же, как и ввод - из углубленных переливных карманов (рис. 14.3, г). Выводная труба должна быть погружена в жидкость во избежание выхода через нее паров.
При использовании двух- и четырех поточных сливов жидкость, как правило, отбирают из карманов центральных сливов.
Корпуса серийно выпускаемых аппаратов для неагрессивных сред изготовляют из углеродистых сталей (ВСтЗсп5, 20К, 16ГС), аппаратов для агрессивных сред - из коррозионно-стойких сталей (08Х22Н6Т, 12Х18Н10Т, 10Х17Н13МЗТ) или из сталей с плакирующим слоем. Кроме того, аппараты можно изготовлять из
чугуна, меди, керамики, стекла и других материалов.
Конструкции контактных массообменных устройств
Тарельчатые контактные устройства можно классифицировать по многим признакам; например, по способу передачи жидкости с тарелки на тарелку различают тарелки с переточными устройствами и тарелки без переточных устройств (провальные).
Тарелки с переточными устройствами имеют специальные каналы, по которым жидкость перетекает с одной тарелки на другую, причем по этим каналам не проходит газ. На провальных тарелках нет переливных устройств, и жидкость, и газ проходят через одни и те же отверстия или прорези в полотне тарелки. Эти прорези работают периодически: в определенный момент времени одни прорези пропускают пар, другие - жидкость; затем их роли меняются.
По характеру взаимодействия газового и жидкостного потоков различают тарелки барботажного и струйного типов. Тарелки, на которых сплошной фазой является жидкость, а дисперсной - газ или пар, называют барботажными. На струйных тарелках дисперсной фазой является жидкость, сплошной - газ; потоки взаимодействуют в прямоточном режиме на поверхности капель и жидкостных струй, взвешенных в газовом потоке.
В зависимости от конструкции устройств ввода пара (газа) в жидкость различают тарелки клапанные, колпачковые, ситчатые, язычковые, решетчатые, с прямоточно-скоростными контактными элементами и др. Одни из этих тарелок могут работать только в барботажном режиме (колпачковые), другие - только в струйном (язычковые), третьи и в том, и в другом режимах (клапанные).
В химической, нефтехимической, нефтеперерабатывающих отраслях промышленности наиболее распространены барботажные и струйные тарелки с переливами.
Колпачковые тарелки с капсульными колпачками до недавнего времени считали лучшими контактными устройствами для ректификационных и абсорбционных аппаратов благодаря простоте эксплуатации и универсальности.
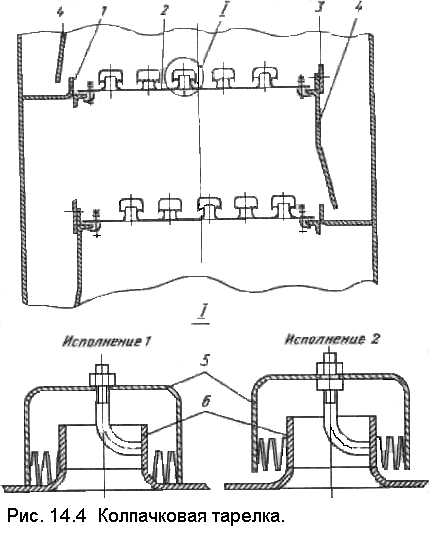
|
Основной частью колпачковой тарелки (рис. 14.4) является стальной диск 1 (или полотно тарелки) с отверстиями для паровых патрубков б. Патрубки приварены к диску. Над патрубками установлены колпачки 5 диаметром 60 или 80 мм. Колпачки имеют прорези высотой 15; 20 или 30 мм.
Для создания необходимого уровня жидкости на тарелке последнюю снабжают сливной перегородкой 3. Переливная перегородка 1 образует переливной карман а, в который погружается сливная планка 4 тарелки, расположенной выше.
|
Применяют два варианта крепления колпачка к тарелке. В исполнении 1 положение колпачка можно регулировать по высоте, в исполнении 2 регулирование невозможно, и нижние кромки прорезей в этом случае упираются в полотно тарелки.
Тарелка работает следующим образом. Поступающая жидкость заполняет тарелку на высоту, определяемую сливной перегородкой 3, при этом прорези колпачков должны быть погружены в жидкость. Пар проходит через паровые патрубки, щели колпачков и барботирует сквозь слой жидкости. Газ и жидкость взаимодействуют в перекрестном токе: жидкость движется по тарелке от переливного кармана к сливной перегородке и далее на расположенную ниже тарелку, а газ - вверх по оси колонны.
Колпачковые тарелки можно изготовлять из чугуна, меди, керамики, углеграфита, пластмасс и др.
Тарелки с капсульными колпачками имеют относительно высокий КПД (0,75-0,80) и работают в широком диапазоне производительностей по газу. Их можно использовать при нестабильных нагрузках по жидкости и пару. Для этих тарелок F »
1 (м/с)/(кг/м3)05, а гидравлическое сопротивление, зависящее от глубины погружения колпачка, не превышает 1 кПа. К недостаткам этих тарелок следует прежде всего отнести значительные металлоемкость и трудоемкость изготовления.
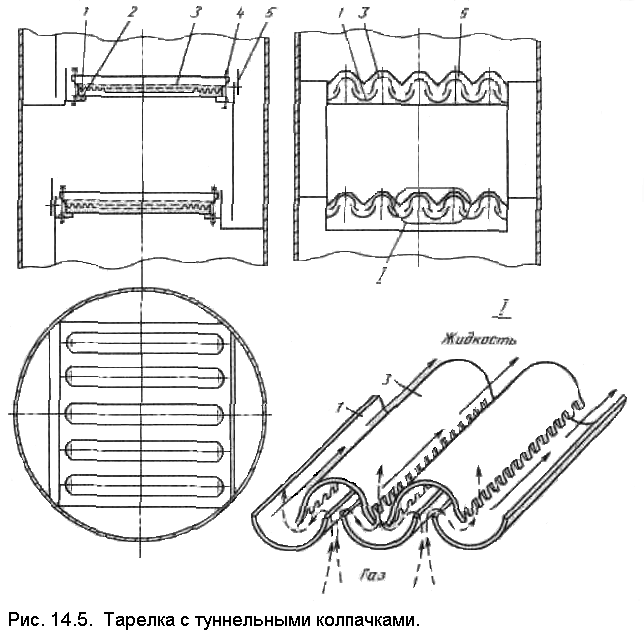
|
В ректификационных аппаратах нефтеперерабатывающих производств используют тарелки с туннельными колпачками (рис. 14.5). Такие тарелки собирают из штампованных желобов /, уложенных по ходу жидкости на опорные уголки 2 и накрытых колпачками 3 так, что между ними образуются паровые каналы. Для равномерного распределения пара колпачки в нижней части имеют трапецеидальные прорези. Колпачки крепят на полотне тарелки шпильками 4. Для равномерного распределения жидкости на тарелке сливную планку 5 также выполняют с прорезями. |
Основное преимущество этих тарелок - небольшое число колпачков и возможность их очистки. Остальные показатели этих тарелок низкие, поэтому в настоящее время их заменяют более современными контактными устройствами.
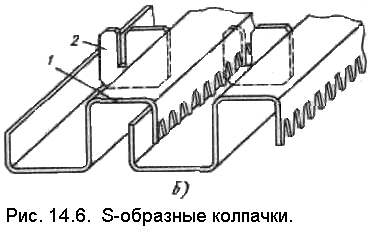
|
В настоящее время в нефтеперерабатывающих колоннах используют и тарелки с S-образными элементами 1 (рис. 14.6), установленными перпендикулярно направлению движения жидкости на тарелке. Для того, чтобы закрыть каналы с торцов и увеличить жесткость тарелки, между S-образными элементами устанавливают пластины 2.
|
В зависимости от диаметра аппарата такие тарелки бывают одно- и многосливными. Характерная особенность этих тарелок состоит в том, что пар выходит из контактных элементов в направлении движения жидкости. Это способствует уменьшению разностей уровней жидкости на тарелке у сливной и переливной перегородок.
Металлоемкость тарелок с S-образными элементами почти вдвое меньше, а производительность на 20-30 % больше по сравнению с тарелками с капсульными колпачками. Эффективность сравниваемых тарелок примерно одинаковая (КПД равен 0,6-0,8).
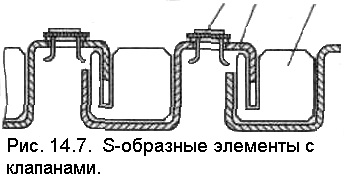
|
Оптимальная нагрузка по газу для этой тарелки на, 10-25 % меньше, чем для колпачковой. Для повышения диапазона устойчивой работы и производительности таких тарелок S-образные элементы (рис. 14.7) снабжают прямоточными клапанами прямоугольной формы, размещенными |
на верхней площадке S-образного элемента. Для увеличения жесткости тарелки устанавливают пластины. По производительности эти тарелки примерно на 10 % превосходят клапанные прямоточные.
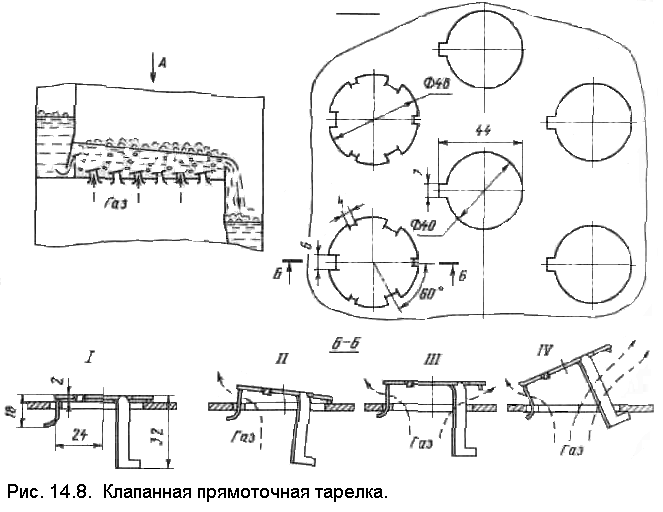
|
Клапанные тарелки также широко применяют в нефтехимической промышленности. Основные преимущества этих тарелок - способность обеспечить эффективный массообмен в большом интервале рабочих нагрузок, несложность конструкции, низкая металлоемкость и невысокая стоимость. Клапанные тарелки изготовляют с дисковыми и прямоугольными клапанами; работают тарелки в режиме прямоточного или перекрестного движения фаз. В отечественной промышленности наиболее распространены клапанные прямоточные тарелки с дисковыми клапанами. На клапанной прямоточной тарелке (рис. 14.8) в шахматном порядке расположены отверстия, в которых установлены саморегулирующиеся дисковые клапаны диаметром 50 мм, способные подниматься при движении пара (газа) на высоту до 6-8 мм.
Дисковый клапан снабжен тремя направляющими, расположенными в плане под углом 45°; две из этих направляющих имеют большую длину. Кроме того, на диске клапана штамповкой выполнены специальные упоры, обеспечивающие начальный зазор между диском и тарелкой; это исключает возможность "прилипания" клапана к тарелке (рис. 14.8, а, положение 1). При небольшой производительности по пару поднимается легкая часть клапана (рис. 14.8, положение //) и пар выходит через щель между клапаном и полотном тарелки в направлении, противоположном направлению движения жидкости по тарелке. С увеличением скорости пара клапан поднимается и зависает над тарелкой (рис. 14.8, положение ///); теперь пар барботирует в жидкость через кольцевую щель под клапаном. При дальнейшем увеличении производительности по пару клапан занимает положение, при котором пар выходит в направлении движения жидкости, уменьшая разность уровней, жидкости на тарелке (рис. 14.8, положение IV). При этом короткая направляющая фиксируется в специальном вырезе на кромке отверстия, обеспечивая заданное положение клапана при его подъеме.
Эффективность клапанных прямоточных тарелок (КПД) 0,70- 0,85, F < 2,5 (м/с)/ (кг/м3)°5, диапазон устойчивой работы 3,5. В области саморегулируемой работы тарелки обладают относительно небольшим гидравлическим сопротивлением.
Клапанная тарелка со штампованными клапанами цилиндрической формы содержит клапана, лежащие на полотне тарелки, и представляющие собой часть цилиндра с ограничителями подъема. Клапан расположен в гнезде, имеющем отогнутую полку. Масса клапана, его конфигурация и положение центра тяжести подобраны так, что при достижении определенной скорости пара клапан перекатывается по поверхности отогнутой полки. При этом между плоскостью тарелки и клапаном образуется щель, через которую в направлении слива жидкости выходит пар. При значительной производительности по пару клапан поднимается и зависает над тарелкой.
В жалюзийно-клапанной тарелке щель для входа газа на тарелку образуется при повороте плоских клапанов-жалюзей вокруг их оси, укрепленной в рамке.
Ситчатые и решетчатые тарелки. Ситчатые тарелки со сливным устройством применяют в колонных аппаратах диаметром 400-4000 мм при расстоянии между тарелками от 200 мм и более. Основной элемент таких тарелок - металлический диск с отверстиями диаметром 2-6 мм, расположенными по вершинам равносторонних треугольников (рис. 14.9).
В колоннах диаметром более 800 мм тарелки состоят из отдельных секций. По креплению секций тарелки к корпусу и устройству переливов такие колонны аналогичны аппаратам с колпачковыми и клапанными тарелками. Преимущество ситчатой тарелки - большое свободное (т. е. занятое отверстиями) сечение тарелки, а следовательно, и высокая производительность по пару, простота

|
изготовления, малая металлоемкость. По производительности по пару (газу) эти тарелки на 30-40 % превосходят колпачковые. Недостаток - высокая чувствительность к точности установки. Аппараты с ситчатыми тарелками не рекомендуется использовать для работы на загрязненных средах; это может вызвать забивание отверстий.
Для уменьшения гидравлического сопротивления и расширения диапазона устойчивой работы ситчатых тарелок их комбинируют с клапанными устройствами; в результате повышается эффективность работы тарелки при малой и большой производительности по пару. При малых нагрузках тарелка работает как обычная |
ситчатая, с увеличением нагрузки открывается клапан, между клапаном и тарелкой образуется щель, откуда под некоторым углом к горизонтали выходит пар, обеспечивая перемещение жидкости по тарелке в направлении слива и уменьшая разность уровней жидкости на тарелке. Ситчато-клапанная тарелка обеспечивает большой диапазон устойчивой работы при небольшом гидравлическом сопротивлении, что делает ее пригодной для процессов, протекающих под вакуумом.
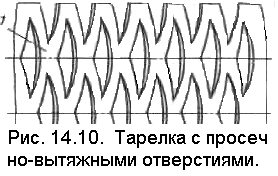
|
Ситчатые тарелки с просечно-вытяжными отверстиями (рис. 14.10) используют в колонных аппаратах диаметром 1200- 4000 мм. Такие тарелки состоят из отдельных секций 1, изготовляемых из листа толщиной 2-3 мм с просечно-вытяжными отверстиями. Тарелка работает как струйная прямоточная. Для уменьшения брызгоуноса под углом 60° |
над тарелкой устанавливают отбойные элементы.
Свободное сечение тарелки, выбираемое из условия отсутствия "провала" жидкости, должно быть достаточно большим (не менее 30 % сечения колонны), чтобы тарелка обладала невысоким гидравлическим сопротивлением. Благодаря этому такие тарелки используют в вакуумных колоннах. Минимальное расстояние между тарелками в колонне 450 мм.
Ситчатые тарелки наиболее распространены в качестве контактных устройств ректификационных колонн воздухоразделительных установок, работающих при низкой температуре. В аппаратах небольшого диаметра применяют S-образные ситчатые тарелки (рис. 14.11). Такая тарелка представляет собой перфорированный лист 1, к которому припаяна S-образная перегородка 3, делящая тарелку на две части. Стекающая с верхней тарелки жидкость через прорези в сливном стакане 2 и далее через переливную перегородку 5 поступает на тарелку и движется в направлении, указанном стрелками, контактируя с паром, поднимающимся через
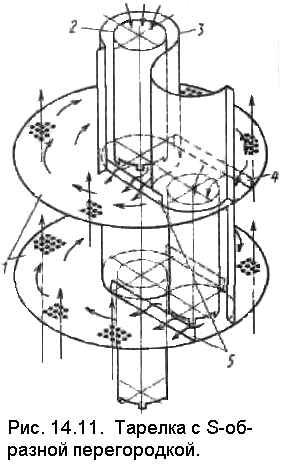
|
отверстия в листе 1. Подойдя к перегородке 3 с другой стороны, жидкость стекает на следующую тарелку через сливную перегородку 4 и сливной стакан.
Решетчатые провальные тарелки используют в установках, рабочая производительность которых отклоняется от расчетной не более чем на 25 %. К преимуществам этих тарелок следует, прежде всего, отнести простоту конструкции и малую металлоемкость. Кроме того, тарелки имеют большую пропускную способность по жидкости и, при достаточной ширине щели, могут быть использованы для обработки загрязненных жидкостей, оставляющих осадок на тарелке. По эффективности решетчатые провальные тарелки обычно не уступают тарелкам с переливом. К недостаткам относятся, узкий диапазон устойчивой работы и сложность обеспечения равномерного |
распределения орошения по поверхности тарелок в начале процесса.
Конструктивно тарелка представляет собой плоский, перекрывающий все сечение колонны диск с выштампованными в нем прямоугольными щелями, уложенный на опорную конструкцию. Обычно площадь прорезей составляет 10-30 % всей площади тарелки. Прорези (как правило, размерами 4x60 мм) располагаются на поверхности тарелки с шагом t = 10 ... 36 мм.
При работе колонны под давлением поступающих паров на полотне тарелки создается слой жидкости, через которую барботирует пар. При этом часть жидкости протекает через прорези на расположенную ниже тарелку. Прорези работают периодически: места стока жидкости и прохода пара произвольно перемещаются по полотну тарелки.
Секционированные массообмечные устройства. Одно из направлений технического прогресса в химической, нефтехимической и нефтеперерабатывающей промышленности - разработка и применение аппаратов большой единичной мощности. До недавнего времени повышение эффективности и производительности колонн обеспечивали увеличением их высоты и диаметра.
Однако с увеличением диаметра колонны возрастает неупорядоченность движения взаимодействующих фаз: на тарелке появляются "байпасные" потоки, "мертвые" зоны, возникает поперечная неравномерность скорости газового потока и высоты жидкости на тарелке. Все это снижает эффективность массообмена в колонне. В связи с этим производительность аппарата следует повышать не увеличением размеров аппарата, а созданием контактных устройств, обладающих высокой производительностью по жидкости и пару, в частности, продольным и поперечным секционированием этих устройств.
Известно, что производительность тарелок повышается при контактировании фаз в прямотоке. Однако при прямоточном взаимодействии и большой скорости пара (газа) жидкость смещается в направлении к сливному карману, что затрудняет работу сливных устройств.
Для компенсации прямоточного движения фаз и исключения его распространения на всю тарелку можно устанавливать на тарелке продольные и поперечные перегородки, обеспечивающие зигзагообразное движение жидкости на тарелке от перелива к сливу, а также создающие условия для движения потоков парожидкостной смеси по тарелке в противоположных или пересекающихся направлениях.
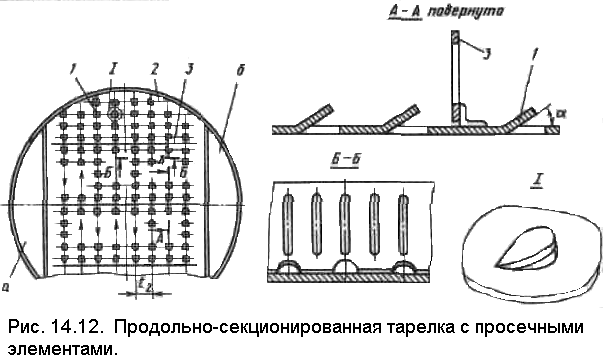
|
|
Примером может служить продольно-секционированная тарелка с просечными элементами (рис. 14.12). На полотне тарелки 2 выштампованы просечки 1, отогнутые под углом а. Тарелка секционирована вдоль потока жидкости вертикальными перегородками 3, причем для создания постоянного гидрав-лического сопротивления по всей тарелке перегородки перфорированы.
При скорости газа до 1,5 м/с тарелки работают аналогично ситчатой и колпачковой: жидкость из переливного кармана а поступает на рабочую часть тарелки, газ вводится через просечки, барботирует через слой жидкости, аэрирует ее и на тарелке образуется газожидкостный слой. При скорости газа более 1,5 м/с газовые струи, выходящие из просечек, и создаваемые ими потоки жидкости движутся к вертикальным перегородкам или стенкам колонны. Ударяются о них, сепарируются и газ покидает тарелку. При этом жидкость совершает сложное зигзагообразное движение от переливного а к сливному 6 карману.
Вариантом массообменного устройства с продольным секционированием является клапанная тарелка с продольными перегородками 3 (рис. 14.13), которая отличается от тарелки с просечными элементами тем, что на полотне 1 тарелки вместо просечек смонтированы клапаны 2 с боковыми стенками, обеспечивающие
направленное движение жидкостного потока.
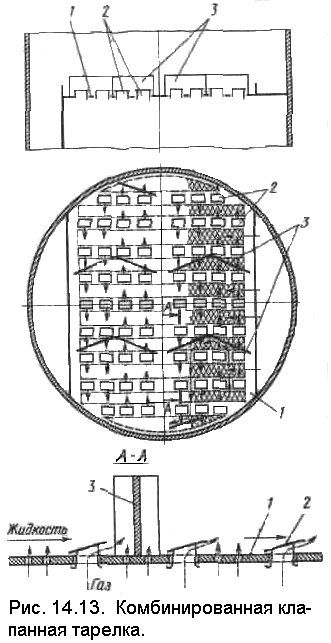
|
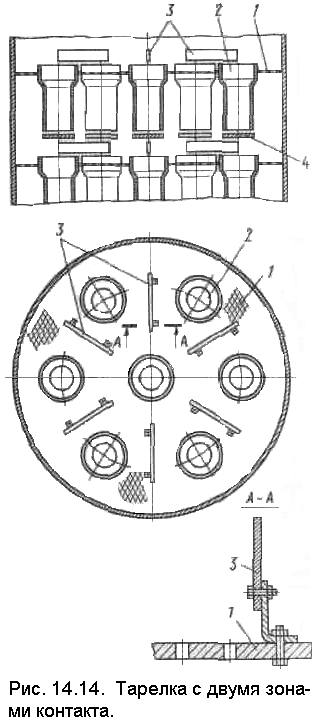
|
По производительности такие тарелки превосходят обычные клапанные тарелки без продольного секционирования в 1,4 раза, а по эффективности массообмена в 1,25-1,3 раза;
При высокой плотности орошения [более 50 м 3/(м2ч)], когда работа тарелок лимитируется производительностью переливных устройств, целесообразно применение многосливной продольно-секционированной тарелки, или тарелки с двумя зонами контакта фаз (рис. 14.14). Последняя представляет собой комбинацию барботажной тарелки (ситчатой, клапанной) с устройством, в котором реализуется зона контакта фаз, формирующаяся в пространстве между тарелками при перетекании жидкости. Тарелка состоит из перфорированного основания 1 с установленными на нем сливными карманами 2 (могут быть одно-, двух- и трехщелевьми), направляющих планок 3 и отбойных дисков 4.
Однощелевой сливной карман, установленный на тарелке 1 (рис. 14.15, а), состоит из патрубка 2 и отбойного диска 3, укрепленного так, что между ними образуется кольцевая щель шириной hщ = 4 ... 12 мм. Через эту щель вытекает
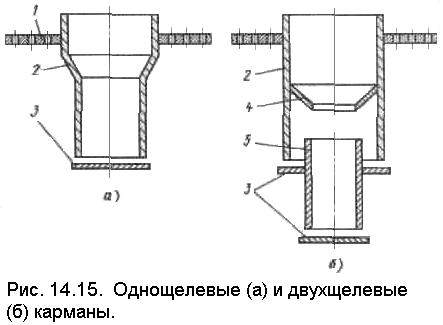
|
кольцевая струя жидкости, образуя дополнительную зону контакта. При установке двухщелевого сливного кармана (рис. 14.15, б) жидкость переливается через сливную перегородку, протекает по внутренней стенке наружного патрубка 2 и конусу 4 во |
внутренний патрубок 5 и вытекает из нижней щели кольцевой струей, образуя дополнительную зону контакта.
С увеличением производительности по жидкости уровень ее в патрубке 5 повышается, жидкость заполняет пространство в патрубке 2 и начинается истечение из верхней щели. В пространстве между тарелками образуется вторая кольцевая струя. Таким образом, многощелевой слив позволяет значительно расширить диапазон нагрузок по жидкости
Насадочные колонные аппараты
Диаметр насадочных колонн обычно не превышает 4000 мм. Для колонн большого диаметра трудно достичь высокой эффективности из-за сложности обеспечения равномерного распределения газовой и жидкой фаз по сечению аппарата. Однако известны отдельные конструкции насадочных аппаратов диаметром до 12 м.
Корпус 1 абсорбционной насадочной колонны (рис. 14.16) выполняют либо цельносварным, либо из отдельных царг с приварными или съемными крышками. Насадочные аппараты весьма чувствительны к неравномерности орошения, поэтому жидкость для орошения насадки подается через распределительную тарелку 2. Насадку 3 располагают по высоте аппарата в несколько слоев (секций) и укладывают на опорные решетки 4. Для загрузки и выгрузки насадки в верхней и нижней частях каждой секции обычно устанавливают люки б и 8. При больших нагрузках по газу и перепаде давлений 400-700 Па на 1 м высоты насадки сверху на каждый слой насадки укладывают удерживающую решетку, предотвращающую выброс насадки. В верхней части колонны размещено отбойное устройство 7. Газ и жидкость движутся в насадочной колонне противотоком. При этом газ вводится в колонну снизу через штуцер А, а выводится через штуцер Б, орошающая жидкость вводится сверху через штуцер В, а выводится через штуцеры Г или Д.
При стекании жидкости по насадке происходит ее перераспределение и на некотором расстоянии от распределитель, ной тарелки равномерность орошения может резко уменьшиться; при этом жидкость течет вдоль стенки аппарата, а
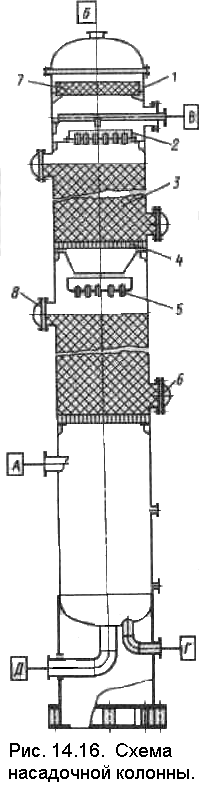
|
центральная часть насадки остается неорошенной. Для исключения этого явления насадочное пространство разделяют на слои и устанавливают между слоями перераспределительные тарелки 5, которые собирают жидкость и распределяют ее вновь по сечению аппарата.
В настоящее время используют насадки различных видов. По существующей классификации их можно отнести либо к регулярной (правильно уложенной), либо к нерегулярной (засыпано: навалом).
Корпус и внутренние устройства серийно выпускаемых насадочных аппаратов изготовляют из тех же материалов, что для тарельчатых массообменных аппарате; Нерегулярную насадку применяют в процессах массообмена, протекающих под давлением или в условиях неглубокого вакуума. Эта насадка обладает рядом преимуществ, одно из которых состоит в практическом отсутствии проблемы выбора материала. Насадку можно изготовить из металлов, полимеров, керамики. Полимерная и керамическая насадка наиболее приемлема для обработки агрессивных сред. Нерегулярная насадка имеет существенные преимущества по сравнению с регулярной по технологии изготовления, транспортирования и монтажа.
По конструктивным признакам эту насадку можно разделить на кольца и седла, хотя в отечественной и зарубежной практике применяют насадочные тела и другой формы.
В настоящее время в отечественной химической и нефтехимической промышленности наиболее распространена нерегулярная насадка в виде колец Рашига и их модификаций. Насадка Рашига имеет небольшую стоимость, но малоэффективна. Эти кольца из металла, фарфора, керамики, пластмасс изготовляют самых различных размеров (диаметр 5-150 мм), хотя в промышленных колоннах чаще |
используют кольца диаметром 25 и 50 мм (рис. 2.27, а). Кольца меньшего размера обладают значительным гидравлическим сопротивлением, большего размера менее эффективны.
Для повышения эффективности массообмена кольцевую насадку изготовляют перфорированной и с внутренними перегородками.

|
В ФРГ предложена кольцевая насадка размером 50x50 мм коррозионно-стойкой стали - так называемые кольца Палля (рис. 14.17, б). На цилиндрической поверхности насадки выштампованы и отогнуты вовнутрь лепестки шириной 10 мм. |
Механическую прочность насадки обеспечивают кольцевые гофры, служаще также для перераспределения жидкости.
Разновидностью колец Палля является выпускаемая в США насадка "Хай-пак", отличающаяся от рассмотренной числом и расположением лепестков. К кольцевой насадке с перфорированной цилиндрической частью и внутренними перегородками относится насадка "Каскад-мини-ринг" (рис.14.17, в).
Отечественная промышленность изготовляет кольцевую нерегулярную насадку в форме колец Рашига, а также кольца Палля из пропилена размерами 50x50 мм и из металла размерами 25х25 и 35x35 мм.
Седлообразная насадка имеет большую удельную поверхность и высокую способность к перераспределению жидкости по сечению колонны. Такую насадку выпускают главным образом виде седел "Инталокс" (рис. 14.17, г) и Берля из керамики и пластмассы. Пластмассовая насадка "Сюпе торус садлес" отличается от седла "Инталокс" наличием отверстий в центре седла, что повышает ее эффективность, и гофр на краях, улучшающих перераспределение жидкости.
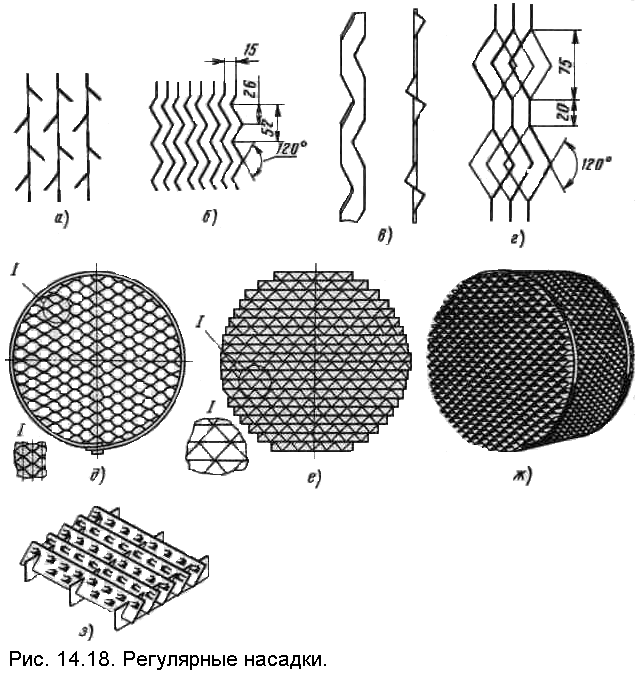
|
Регулярная насадка (правильно уложенная) отличается от нерегулярной меньшим гидравлическим сопротивлением и поэтому особенно пригодна для процессов вакуумной ректификации. К недостаткам аппаратов с регулярной насадкой нужно отнести их высокую чувствительность к равномерности орошения.
Простейшая регулярная насадка - плоскопараллельная (рис. 14.18) - представляет собой пакеты, набираемые из плоских вертикальных, обычно металлических пластин толщиной 0,4-1,2 мм, расположенных параллельно с одинаковым зазором 10- 20 мм. |
Высота пакета пластин 400-1000 мм. Наружный диаметр пакета соответствует внутреннему диаметру колонны Dв. Для повышения равномерности распределения жидкости в колонне пакеты устанавливают один над другим взаимно повернутыми на угол 45-90°. Насадка может устойчиво работать в широком диапазоне производительности по газу [F = 3,5 ... 8 (м/с)/(кг/м3)05] и по жидкости [L = 0,3 ... 50 м3/(м2-ч)1. В зависимости от производительности насадка обеспечивает высоту, эквивалентную одной теоретической ступени, в пределах 0,6-1,5 м при гидравлическом сопротивлении 1 м насадки 70-300 Па. Недостатки этой насадки - высокая металлоемкость, плохое перераспределение жидкости, сравнительно низкая эффективность. Для устранения последнего недостатка листы плоскопараллельной насадки выполняют с рифлением или с различными турбулизирующими элементами. Так, насадка конструкции ЛТИ им. Ленсовета (рис. 14.19, а) состоит из вертикальных, параллельно расположенных листов, имеющих поперечные окна с отогнутыми лепестками; соседние по высоте лепестки отогнуты в противоположные стороны и делят колонну в продольном направлении на контактные камеры. Газ, поднимаясь по колонне, проходит через камеры, многократно меняя направление движения при ударе о лепестки. Жидкость, стекая по насадке с лепестка на лепесток, распыляется восходящим газовым потоком.
Основное преимущество гофрированной насадки (рис. 14.18, б), состоящей из вертикальных металлических листов с рифлением, по сравнению с плоскопараллельной насадкой - меньший брызгоунос. Это объясняется тем, что гофрированная насадка беспровальна. Зазоры между листами иногда обеспечивают дистанциоными планками (рис. 14.18, б), установленными вертикально на расстоянии 250 мм одна от другой и приваренными к листам точечной сваркой.
Разновидностью гофрированной насадки является Z-образная насадка, изготовляемая из перфорированного листа (рис. 14.18, г). По основным технологическим параметрам эта насадка на 15- 20 % превосходит плоскопараллельную.
Щелевая, или сотовая насадка (рис. 14.18, д) образована из гофрированных вертикальных листов, сдвинутых один относительно другого так, что по высоте пакета образуются изолированные вертикальные каналы. Листы соединены в пакеты высотой 400-1000 мм точечной сваркой. К преимуществам этой насадки относятся значительно более высокая (в 2-3 раза), чем плоскопараллельной насадки, удельная поверхность, а также возможность нагревать или охлаждать контактирующие фазы, поскольку каналы, образованные гофрами, пригодны для подачи в них теплоносителя или хладагента. К недостаткам насадки следует отнести неравномерность толщины пленки жидкости в канале. Накопление жидкости в углах канала несколько ухудшает эксплуатационные качества этой насадки.
Таблица 14.1 Сравнительная характеристика насадок различных типов
Тип насадки
|
Производительность
|
Эффективность
|
Гидравлическое сопротивление
|
Кольца Рашига ( d = 25 мм)
|
1
|
1
|
1
|
Кольца Палля (d = 25 мм)
|
1,4-1,5
|
1,00-1,25
|
0,70-0,75
|
Седла Берля
|
1,08-1,25
|
1,11
|
0,6-0,7
|
Седла "Инталокс"
|
1,2-1,4
|
1,3
|
0,45-0,50
|
"Гудлоу"
|
1,15-1,20
|
3,5
|
0,13
|
"Зульцер" |
"2
|
2,5
|
0,25-0,45
|
Хорошие характеристики имеют насадки из проволочной сетки. Примером может служить насадка Гудлоу - пакеты свернутой в рулон гофрированной проволочной сетки (диаметр проволоки 0,1 мм). Гофры расположены под углом 60° к вертикали, высота пакета насадки 100-200 мм.
В России насадка из гофрированной сетки (рис. 14.18, е) используется для процессов ректификации, проводимых под вакуумом. Пакеты такой насадки высотой 150-200 мм изготовляют из тканой проволочной сетки толщиной 0,2 мм.
Последнее время за рубежом разработаны различные виды новой высокоэффективной насадки, способной работать при удельной нагрузке по жидкости L< 200 м3/(м2ч) и F = 5 ... 8 (м/с)/(кг/м3)°5. Насадка обеспечивает значительное (до 5-6) число теоретических ступеней на 1 м высоты и небольшое гидравлическое сопротивление (до 150 Па на 1 м высоты). Примерами может служить насадка "Импульс пакинг" из металла и полимерных материалов, насадка "Зульцер" (рис. 14.18, ж) из гофрированной сетки толщиной 0,16 мм, а также регулярная насадка "Роли пак", образованная ярусами наклонных листов с прорезями (рис. 14.18, з).
В таблице 14.1 дана сравнительная характеристика насадок различных видов.
Область применения насадок. При выборе насадки для проведения конкретного процесса контактирования в системе пар (газ)-жидкость руководствуются обычно следующим правилом: регулярную насадку, гидравлическое сопротивление которой меньше, чем нерегулярной, используют в процессах вакуумной ректификации, нерегулярную - в процессах неглубокого вакуума и под давлением. Регулярной насадке отдают также предпочтение при обработке продуктов, время пребывания которых в аппарате ограничено, например, из-за склонности к разложению.
Регулярную насадку используют в вакуумных стальных колонных аппаратах диаметром 400-3600 мм, предназначенных для разделения термически нестойких и легко полимеризующихся органических смесей при остаточном давлении рабочей среды 0,25-98 кПа и температуре от 0 до 300 °С. Области применения основных типов насадок указаны в табл. 14.2.
Таблица 14.2 Области применения насадок
Тип насадки
|
Область применения |
Плоскопараллельная |
Процессы ректификации, требующие до пяти теоретических ступеней разделения и перепада давлений на одну теоретическую ступень до 0,06 кПа |
Сотовая |
Процессы ректификации, требующие до 15 теоретических ступеней разделения и перепада давлений на одну теоретическую ступень до 0,05 кПа |
Из гофрированной сетки |
Процессы ректификации чистых жидкостей, требующие большого числа (более 15) теоретических ступеней разделения и перепада давлений на одну теоретическую ступень до 0,03 кПа |
Z-образная |
Процессы ректификации и абсорбции загрязненных жидкостей, требующие до 15 теоретических ступеней разделения и перепада давлений на одну теоретическую тарелку до 0,05 кПа |
При выборе типа аппарата, работающего при атмосферном или повышенном давлении, необходимо учитывать следующее. В аппаратах с регулярной насадкой обеспечивается больший F-фактор, чем при использовании нерегулярной насадки. Однако максимальная нагрузка по жидкости в аппаратах с нерегулярной насадкой достигает 300м3(м2ч), что почти на 30 % больше, чем для аппаратов с регулярной насадкой.
При небольшой нагрузке по газу [ F = 4...5 (м/с)/(кг/м3)°5] допустимо и целесообразно использование нерегулярной насадки. При больших объемах газа необходимо использовать регулярную насадку с каналами, обеспечивающими преимущественный проход газовой фазы. Поскольку обычно F-фактор меняется по высоте колонны, можно использовать аппараты с комбинированной насадкой: в той части аппарата, где F-фактор меньше, размещают нерегулярную насадку, а там, где F-фактор больше,- регулярную. Таким образом, можно обеспечить оптимальные условия работы по всей высоте колонных аппаратов.
Экстракционные колонные аппараты
Жидкостную экстракцию, т. е. - процесс разделения жидких компонентов с помощью жидкого растворителя (экстрагента), широко применяют в процессах переработки нефти, для разделения ароматических и алифатических углеводородов, для обезвоживания уксусной кислоты, при разделении редкоземельных элементов и др. Процесс экстракции осуществляется в аппаратах, называемых экстракторами.
Экстракторы, в которых взаимное движение и сепарация контактирующих фаз генерируется силами гравитации, называются гравитационными, или колонными, в отличие от центробежных экстракторов, где взаимодействие и сепарация фаз обусловлены полем центробежных сил.
Колонные экстракторы для системы жидкость-жидкость разделяют на аппараты без подвода энергии и с подводом энергии. К первым относятся распылительные, насадочные и ситчатые экстракторы, ко вторым - смесительно-отстойные, роторные, пульсационные, вибрационные и др.
Распылительные экстракционные аппараты представляют собой полые колонны, в которых одна из фаз движется сплошным потоком, а другая - в виде капель. Эти аппараты просты по конструкции, но мало эффективны. Насадочные экстракционные колонны по конструкции аналогичны рассмотренным выше насадочным колоннам для процессов ректификации и абсорбции. В качестве насадки в них используют преимущественно кольца Рашига, которые укладывают на опорные решетки колосникового типа.
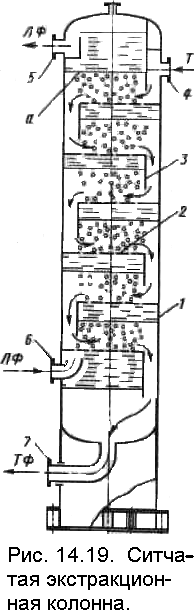
|
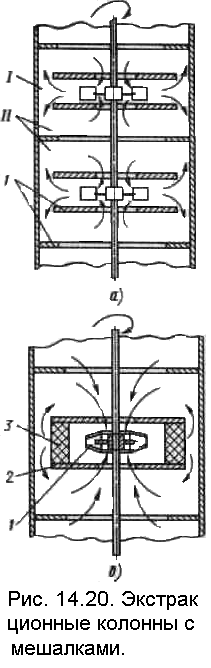
|
Ситчатая экстракционная колонна (рис. 14.19) имеет вертикальный цилиндрический корпус 1 и перфорированные (ситчатые) тарелки 2, снабженные переливными устройствами 3. Колонна работает следующим образом. Тяжелая фаза ТФ через штуцер 4 подается непрерывно в колонну, сплошным потоком опускается по колонне и удаляется через штуцер 7. Легкая фаза ЛФ непрерывно поступает через штуцер 6 в колонну под нижнюю тарелку 2. Проходя через отверстия тарелки, эта фаза диспергируется и в виде капель поднимается под следующую тарелку. В верхней части дисперсная фаза коалесцирует в сплошной слой, образуя уровень раздела фаз а и удаляется через штуцер 5. В процессе образования капель и их движения осуществляется процесс массообмена.
Из аппаратов, работающих с подводом энергии, выделим прежде всего роторные экстракторы.
Одной из первых конструкций роторных экстракторов является колонна Шайбеля, состоящая из чередующихся смесительных и отстойных секций. Для перемешивания в смесительных секциях размещены закрепленные на валу мешалки. Отстойные секции заполнены насадкой (плетеной сеткой с крупными ячейками).
В конструкции, показанной на рис. 14.20, а, смесительная секция I изолирована от отстойной секции II горизонтальными статорными кольцами 1. В более поздних конструкциях колонн Шайбеля (рис. 14.20, б) перемешивание фаз осуществляется турбинными мешалками 1 в зоне между неподвижными кольцевыми перегородками 2 и слоем проволочной сетки 3.
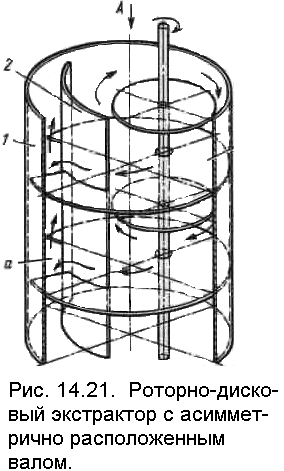
|
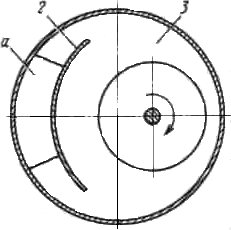
|
Роторно-дисковый экстрактор представляет собой колонну, по оси которой установлен ротор в виде вертикального вала с круглыми горизонтальными дисками. Диски вращаются в полости секции, образованной закрепленными на
корпусе статорными кольцами 3. Ротор приводится во вращение от электропривода 4. Легкая фаза ЛФ вводится в аппарат снизу, а тяжелая ТФ - сверху.
Под действием вращающихся дисков фазы в секциях совершают сложное циркуляционное движение, при котором совмещены радиальное и осевое движение жидкости. Дисперсная и сплошная фазы движутся противотоком; капли дробятся дисками, отбрасываются на периферию колонны, сталкиваются со стенками колонны и между собой. Одновременно с дроблением капель происходит их коалесценция.
На рис. 14.21 показан роторно-дисковый экстрактор с асимметричным расположением вала. В корпусе 1 аппарата смесительные секции отделены одна от другой статорными кольцами 3. Из одной секции в другую фазы перемещаются через отстойные зоны а, отделенные от смесительных зон вертикальным экраном 2.
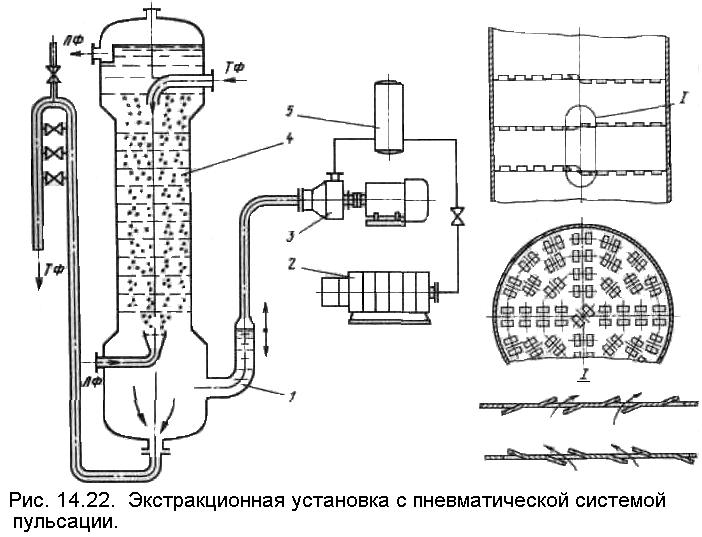
|
В пульсационных экстракторах интенсификацию массообмена между контактирующими фазами обеспечивают сообщением им колебательного движения определенных амплитуды и частоты. Независимо от типа насадки экстракционную колонну в этом случае снабжают генератором пульсаций (пневматическим, механическим и др.) Так, в установке с пневматической системой пульсаций (рис. 14.21) воздух или инертный газ от компрессора 2 через ресивер 5 и золотниково-распределительный механизм 3 пневматического пульсатора поступает в пульсационную камеру 1 экстрактора 4. При прямом импульсе уровень жидкости в пульсационной камере снижается, вследствие чего жидкость в колонне поднимается при обратном импульсе-камера соединяется с атмосферой и жидкость в колонне опускается. В аппаратах этого типа не требуется устанавливать переливные устройства на тарелках, так как при подъеме столба жидкости в колонне через отверстие тарелки проходит легкая фаза ЛФ, а при опускании - тяжелая фаза ТФ.
В пульсационных экстракторах используют обычно ситчатые тарелки, а также тарелки типа КРИМЗ. Последняя более эффективна и представляет собой плоский- диск, на котором отштампованы прямоугольные отверстия с отбортовкой в виде наклонных направляющих лопаток. Отверстия размещены по концентрическим окружностям, причем лопатки соседних тарелок наклонены в противоположные стороны.
В вибрационных экстракторах эффективный массообмен обеспечивается возвратно-поступательным движением пакета перфорированных тарелок, через которые жидкость проталкивается в виде распадающихся на капли струй. В отличие от пульсаций столба жидкости вибрации тарелок происходят с меньшей амплитудой и большей частотой.
На рис. 14.23 показан вибрационный экстрактор. Как и в пульсационных аппаратах, тяжелая ТФ и легкая ЛФ фазы движутся противоточно. В верхней части колонны 1 размещен электропривод 4 с эксцентриком 5. При вращении вала эксцентрик передает возвратно-поступательное движение штоку 2, с которым жестко соединены перфорированные тарелки 3.
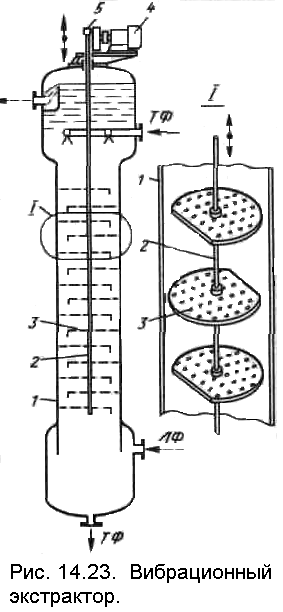
|
|